If you’re working on or alongside teams using Six Sigma, you may have heard of DMAIC or read about it before. However, to take advantage of DMAIC, you may need a brief refresher on what the term means and the different steps involved.
This article provides a comprehensive understanding of DMAIC and its application within Six Sigma. We’ll discuss:
What is DMAIC?
DMAIC (pronounced "de-may-ick") is a structured, five-step process improvement methodology that forms an integral part of the Six Sigma framework. The acronym itself guides the process: Define, Measure, Analyze, Improve, and Control. This systematic approach is designed to help organizational teams refine their existing processes for the best possible outcomes.
Originally conceptualized within manufacturing by Toyota, DMAIC has evolved significantly. Today, both DMAIC and the broader Six Sigma methodology are widely adopted by businesses across diverse industries. They serve as a robust, data-driven approach to continuous improvement, enabling companies to identify root causes of inefficiencies, implement targeted solutions, and sustain long-term enhancements to their operations.
What are the five phases of DMAIC?
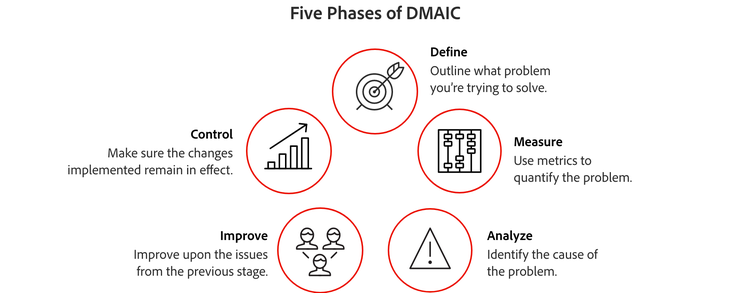
Let’s look at each of these five steps in a little bit greater detail.
Define.
The define phase aims to outline what problem you’re trying to solve. At this stage, teams should determine the goal of the process improvement cycle, identify who the process will benefit, and define what success would look like. A value stream map can help visualize and analyze the present state of the entire process.
Measure.
The goal of the measure phase is to quantify the problem. Your team needs to determine how well the current process works, identify the key metrics to monitor throughout the process, and specify what data will be collected. Data should be gathered from each step along the way to identify opportunities for improvement.
Analyze.
During this phase, you identify the cause of the problem. Teams analyze the data they collected to identify areas that need improvement and the reasons behind them. Root cause analysis can be helpful during this phase of the process as an actionable structure for thinking about a problem and identifying the best way to solve it.
Improve.
In this phase, your goal is to address the issues identified in the previous stage. The team needs to work together to identify and address the root causes of problems within the process. Once issues are identified, the team needs to verify the results and adjust if improvement doesn’t happen.
Control.
The control phase ensures that the changes implemented during the process remain in effect. A control plan documents the process. This includes metrics to measure success, which can be used by future teams or in future versions of a process.
How to start using DMAIC for process improvement.
Implementing a DMAIC initiative can seem like a significant undertaking, but it represents a powerful strategy for driving sustained process improvement within your organization. To effectively leverage this methodology and ensure its success, consider these foundational steps:
1. Assess your project's suitability.
Before committing to DMAIC, it's crucial to evaluate whether it aligns with the specific challenge you face. DMAIC is ideally suited for complex, persistent problems where the root cause is not immediately apparent and requires a data-driven investigation. If the solution to a problem is already known or straightforward, a less intensive problem-solving approach might be more efficient. Ensure your team comprehends the structured five-phase commitment inherent in DMAIC.
2. Identify the Right Pilot Project.
For your initial foray into DMAIC, selecting an appropriate project is key to building momentum and demonstrating value. Choose a project that is:
- Manageable in scope: Choose a well-defined problem that can realistically be addressed within a practical timeframe, typically a few months.
- Measurable: The problem should have quantifiable metrics that allow for a clear assessment of current performance and enable the objective measurement of improvements.
- Impactful: While manageable, the project should deliver tangible benefits that are significant enough to showcase DMAIC's effectiveness to organizational stakeholders, thereby fostering broader adoption.
- Supported by a sponsor: Secure a dedicated leader or stakeholder who champions the project, providing necessary resources and overcoming potential roadblocks.
3. Assemble your team.
Successful DMAIC implementation relies on a collaborative, multidisciplinary team. For your chosen project, select individuals with diverse expertise, typically including:
- A process owner with deep insight into the current process to verify if it improves over time.
- Team members who possess analytical capabilities to manage and interpret data.
- Individuals who will be directly involved in implementing and sustaining the improvements.
- A DMAIC Green Belt or Black Belt to serve as a coach, guiding the team through each phase of the methodology.
4. Secure leadership buy-in.
Effective DMAIC initiatives often require allocation of resources, dedicated time, and cross-departmental cooperation. Present your proposed project to organizational leadership, clearly articulating the problem, the anticipated benefits, and the necessary resource commitments. Gaining their explicit endorsement is vital for legitimizing the effort and ensuring consistent support throughout the project lifecycle.
5. Cultivate a data-driven mindset.
At its core, DMAIC is a scientific approach to problem-solving, grounded in data. From the outset, commit to rigorous, accurate data collection during the Measure phase. This empirical foundation will underpin your analysis, inform your solutions, and validate the impact of your improvements. Encourage your team to continually ask "why" to uncover the actual root causes, allowing objective data to inform every decision.
By executing these foundational steps, your organization can successfully initiate its journey with DMAIC, cultivating a culture of continuous operational excellence and fact-based decision-making.
DMADV vs DMAIC.
Both DMAIC and DMADV are robust, data-driven methodologies within the Six Sigma framework, designed to drive quality and efficiency. While they share the overarching goal of achieving excellence, their applications hinge on a crucial distinction: whether you're optimizing an existing asset or creating a brand new one.
- DMAIC (Define, Measure, Analyze, Improve, Control) is utilized when you need to improve an existing process or product that is underperforming. It's a systematic approach to problem-solving that reduces defects, enhances efficiency, or optimizes an existing process.
- DMADV (Define, Measure, Analyze, Design, Verify), conversely, is employed when you need to design a brand-new product, service, or process from scratch, or if an existing one is so fundamentally flawed that it requires a complete redesign. Its objective is to ensure that the new design meets customer requirements and quality standards from its very inception.
In essence, if you aim to enhance what you currently have, you'll leverage DMAIC. However, if you're building something new or require a fundamental overhaul, DMADV is the methodology for designing quality in from day one.
Adobe can help support DMAIC process improvement.
Workfront is an enterprise work management software that supports Six Sigma and DMAIC process improvement methodologies. Workfront enables your teams to collaborate and find creative solutions to process improvements. Implementing DMAIC is easier with Workfront.
To learn more about Workfront, watch the overview video now.
Recommended for you
https://business.adobe.com/fragments/resources/cards/thank-you-collections/workfront