
Elevating design in sports.
Mizuno improves shoe development and marketing with 3D data from the Adobe Substance 3D Collection.
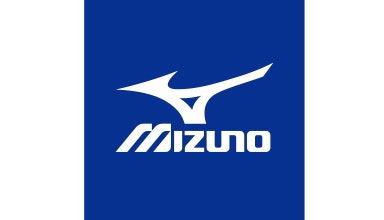
Reduce sample creation time by weeks while eliminating materials waste and transport costs
Objectives
Accelerate product design and review cycles
Reduce the number of physical samples manufactured
Use 3D data across commerce, marketing, and photography
Reach sustainability goal of becoming carbon neutral by 2050
Results
Speeds time to design new shoes
Reduces the number of samples created, decreasing carbon footprint
Encourages more experimentation, leading to more creative designs
Eliminates photo shoot cost and time by using 3D models to create virtual photographs
When the Mizuno brothers started their sports business almost 120 years ago, they had one goal: to create something great. Today, Mizuno is known for its quality sports equipment and sportwear made for everyone, from weekend athletes to Olympians, in a range of sports from running to football to golf.
Mizuno sports shoes combine high functionality with eye-catching designs, attracting both top athletes and fashionistas. Designers take up to a year to design each shoe ahead of semi-annual exhibitions, with multiple color variations created for markets around the world. To keep up with growing global demand for designs, Mizuno started migrating from physical samples to 3D virtual samples.
With the addition of Adobe Substance 3D Collection to the 3D design workflow, Mizuno is creating realistic 3D designs in less time. In addition to eliminating the time and cost of sample creation, Mizuno also uses 3D models to support digital commerce and marketing.

“Adobe Substance 3D Collection enables us to be more creative with our designs and continue to create great products for our customers.”
Mr. Takashi Nakamura
Technical Designer, Design Section, Global Footwear Product Division, Mizuno Corporation
Photoreal images in an hour
Sports shoes offer unique design challenges, combining both fashion and product design choices. The soles are typically made of rubber with intricate patterns added for grip, support, and aesthetics. The uppers are softer, often utilizing layers of mesh, leather, reflective fabrics, and other unusual materials. When preparing to create 3D renders of shoes, getting the right combination of colors and textures is critical.
“Adobe Substance 3D Painter makes it easy to apply colors, textures, and even small wrinkles or scratches that make the shoes look more realistic,” says Mr. Takashi Nakamura, Technical Designer, Design Section of Mizuno’s Global Footwear Product Division. “Adding details such as bumps and wear as materials, rather than baking them into the 3D models, allows us to use simpler models with fewer polygons. These low-poly 3D models are more versatile as we can more easily reuse them on other projects, such as websites, catalogs, and marketing.”
Mizuno converted its fabric swatches into 3D materials using Substance 3D Sampler. Designers can take these real-life scans and apply them in different ways to bring ideas to life, such as layering multiple materials, changing colors, and applying materials to specific areas of the render.
The node-based material creation workflow in Substance 3D Designer is particularly helpful when creating more advanced, custom materials for shoes. Designers use node-based graphs to generate repeating patterns, such as fabric mesh or lines of tread on the soles of shoes. If they want to change the pattern, such as widening spaces, they can simply adjust the numbers to generate a new pattern, rather than trying to paint again from scratch.
“Even though we’re working in 3D, the workflow feels very similar to something like Photoshop,” says Ms. Ikuko Okada, Footwear Designer, Design Section of Mizuno’s Global Footwear Product Division. “It took me less than a month to learn how to use Substance 3D apps. Now we can apply designs to a shoe much faster compared to 2D.”

“It took me less than a month to learn how to use Substance 3D apps. Now we can apply designs to a shoe much faster compared to 2D.”
Ms. Ikuko Okada
Footwear Designer, Design Section, Global Footwear Product Division, Mizuno Corporation
Fast and sustainable virtual samples
The ability to create photoreal virtual samples changes how Mizuno approaches the entire design process. Shoe designers no longer work with 2D sketches, exploring their designs directly in 3D.
“The traditional design process bounces between 2D and 3D,” explains Ms. Ayuri Tsunoda, Footwear Designer, Design Section of Mizuno’s Global Footwear Product Division. “We think of the shoe in 3D, but then we would sketch it in 2D and wait for a 3D sample. There were frequent miscommunications where the sample wasn’t quite what we were imagining. We no longer have those issues with 3D virtual samples because everyone can see exactly what the designer’s vision is.”
The process of making physical prototypes often took several weeks and required a lot of material, labor, and shipping costs. Switching to virtual samples eliminates waste, helping Mizuno reach its sustainability goal of becoming carbon neutral by 2050.
Mizuno can now approve a shoe design much faster. Designers share virtual samples with colleagues anywhere in the world. They can make adjustments, such as changing colors, in minutes. Because designers don’t need to worry about spending a lot of time, materials, and money on manufacturing prototypes, they can be more experimental, sometimes creating designs that turn into surprise hits with customers.
Mizuno can start using these virtual samples in catalogs, e-commerce sites, and marketing campaigns, without needing to wait for manufacturers to deliver shoes and set up photo shoots. “Using 3D models, we create more images that appeal to customers,” says Mr. Tomonori Namba, Former Chief of the Planning, Development, and Design Department of Mizuno’s Global Footwear Product Division. “We can try out new visuals without needing to set up a new photo shoot. We can even create images that are more dynamic than real photography, showing off the shoes from dramatic angles.”

“We think of the shoe in 3D, but then we would sketch it in 2D and wait for a 3D sample. There were frequent miscommunications where the sample wasn’t quite what we were imagining. We no longer have those issues with 3D virtual samples because everyone can see exactly what the designer’s vision is.”
Ms. Ayuri Tsunoda
Footwear Designer, Design Section of Global Footwear Product, Mizuno Corporation
Leveraging versatile 3D models
With Adobe helping to make 3D more accessible, Mizuno is expanding its use of 3D models across the company. The equipment and apparel teams are starting to use virtual samples, and buyers looking at digital catalogs can see a 360 degree view of shoes. Mizuno is also exploring the possibilities of VR and AR technology, such as selling products in the metaverse.
“We will never completely eliminate physical samples because we will always need to test the feel and performance of our sports shoes with athletes. However, working with virtual samples allows us to accelerate the design process,” says Mr. Nakamura. “Adobe Substance 3D Collection enables us to be more creative with our designs and continue to create great products for our customers.”
Recommended for you
Content as a Service - Monday, April 3, 2023 at 11:11 (no-lazy)