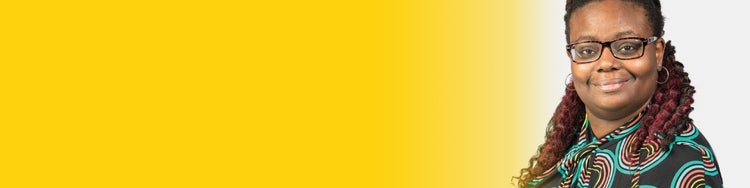
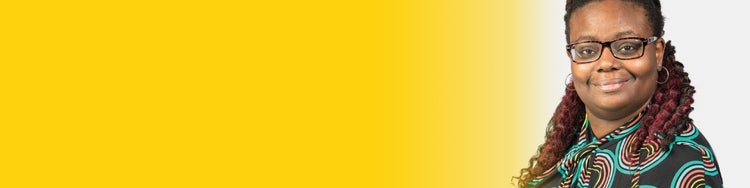
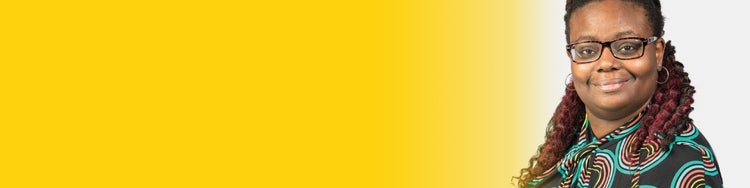
Stanley Black & Decker eliminates redundancies and increases productivity with Workfront.

New Britain, Connecticut
Connected and automated work processes
Products:
Objectives
Eliminate disconnected tools
Reduce busy work for team members
Improve collaboration among 10 separate teams throughout the organization
Results
Connected and automated work processes
Focused work to improve the bottom line
Enabled teams to work together on the same system
Busy work is the thief of efficiency. With Adobe Workfront, Monique Evans, the System Operations Manager at Stanley Black & Decker, has been able to remove busy work for people on her team. The result is a more efficient environment that allows employees to focus on what really matters: work that improves the bottom line.
Monique seized the opportunity to integrate platforms that were already in use, such as the print MIS platform, Avanti Slingshot. No longer would they have to manually duplicate information about print jobs in multiple systems (both Workfront and Avanti Slingshot), or retroactively run reports from the print jobs and input data creating an unmanageable workload.
With Workfront, these problems would become obsolete. Teams would be able to move jobs through from strategy to delivery, quicker and with ease. With Workfront, Stanley Black & Decker can now retain control and visibility of their reports, without the headache or hassle of analog processes.
While setting up the integration with Workfront and Avanti Slingshot, Evans got creative and realized there was even more she could do for her team with Workfront.
“It was a task that people kept forgetting to do, but now they don’t even have to think about. It’s something small, but it definitely helps.”
Monique Evans
System Operations Manager, Stanley Black & Decker
Historically, Evans' team manually entered and updated existing Workfront data when they completed a task. Seeing an opportunity with Workfront, Evans devised a way to remove this manual update and increase efficiency for each task.
Notifying sponsors of project updates and sending project requestors tracking numbers, were once manual tasks requiring additional designer hours. With Workfront these tasks are now completely automated.
“It was a task that people kept forgetting to do, but now they don’t even have to think about. It’s something small, but it definitely helps,” says Evans.
Using a specified set of criteria, Workfront uses data from within projects and tasks to create an update that delivers the tracking number to the requestor, without the designer ever needing to remember this step. Now designers are free to continue on to what they do best: creative work.
Workfront also helps with reporting and tracking dates and turn-around times for each project, helping Evans manage work more easily.
Productivity has also increased, resulting in a business that is both highly efficient and vastly more effective.
With the seemingly unlimited possibilities for connecting Workfront to external systems, Evans is also working on connecting Workfront to their in-house print system and planning for even more integrations as the business moves forward.
With Workfront, Stanley Black & Decker can now retain control and visibility of their reports, without the headache or hassle of analog processes.