Organizations hindered by hidden inefficiencies, such as wasted time, squandered materials, unnecessary motion, and underutilized talent, can struggle to achieve both short-term and long-term business goals. This waste, often embedded in daily routines, impacts the bottom line and stifles innovation.
The critical question for leaders is not whether this waste exists, but how to systematically identify and eliminate it. A solution to this problem lies in the 5S methodology. Born from the Toyota Production System, 5S was meticulously designed to create and maintain a clean, organized, safe, and high-performance work environment. It is a sophisticated management system that removes barriers blocking production efficiency, fostering a deeply ingrained culture of continuous improvement, also known as Kaizen.
This article provides an exhaustive guide to the 5S methodology. We will begin by deconstructing the core principles of 5S, offering a pillar-by-pillar analysis of its framework. We will then present the tangible benefits of 5S, from productivity gains to significant cost savings.
In this post, you’ll learn:
What is 5S?
5S is a methodology for organizing a workspace. The 5S pillars stand for “Sort,” “Straighten” (also called “Set in Order”), “Shine,” “Standardize,” and “Sustain.” Some practitioners now also include a sixth S, which stands for “Safety.”
Toyota initially developed the 5S system, a component of the Lean methodology. However, since its creation, 5S has been adopted by businesses across a broad range of industries.
Virtually any manufacturing company can benefit from implementing 5S. Some of these benefits include:
- Decreased costs
- Greater productivity
- Improved product quality
- Increased safety
- Enhanced equipment longevity
5S is not a one-time clean-up or a superficial tidiness initiative. The 5S methodology is a continuous process designed to achieve transformation. It systematically builds operational discipline from the ground up, making continuous improvement a daily habit rather than a special project. The successful sustainment of 5S often reveals an organization's underlying capacity for constant improvement.
Conversely, a failure to maintain 5S standards can signal deeper cultural resistance to change, making it a powerful leading indicator of an organization's readiness for more complex transformations, such as full-scale Lean adoption or enterprise-wide digital transformation. When an organization cannot sustain 5S, it is rarely a failure of the tool itself, but rather a symptom of deeper organizational issues such as a lack of leadership commitment or poor employee engagement.
5S Methodology.
Professionals at Toyota developed the 5S methodology and associated Lean manufacturing framework.
The creators of the framework aimed to address multiple business challenges. Specifically, they aimed to reduce non-value-adding time, enhance work efficiency, promote safety, and optimize organizational effectiveness.
The methodology was built on these five Japanese words:
-
Seiri (Sort – Eliminate unnecessary actions and wasteful behaviors)
-
Seiton (Straighten – Organize the remaining equipment, inventory, and machinery)
-
Seisou (Shine – Clean, inspect, and enhance the work area)
-
Seiketsu (Standardize – Develop clear and concise standards for the 5S framework)
-
Shitsuke (Sustain – Consistently apply the newly defined 5S standards)
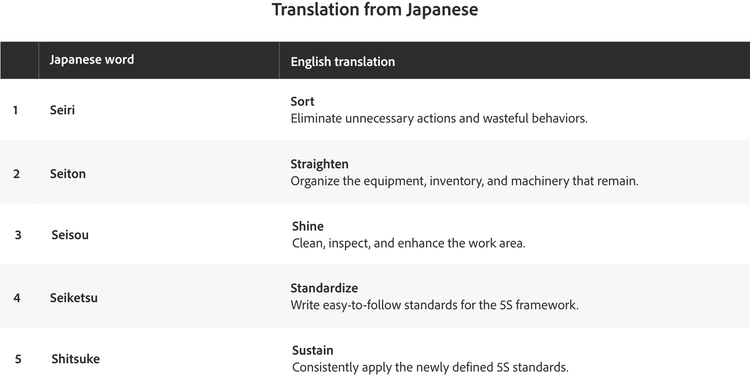
1. Sort.
Seiri or Sort focuses on systematically distinguishing between necessary and unnecessary items within a workspace and ruthlessly eliminating the latter. The primary goal is to eliminate all forms of clutter, whether obsolete tools, excess inventory, outdated paperwork, or redundant digital files, that create physical and cognitive distractions, hinder efficient workflow, and pose safety hazards.
A critical tool for executing the Sort phase is the red-tagging process. This method provides a structured and visual way to manage the identification and disposition of questionable items. The process involves a team systematically evaluating every item in a designated area, asking a series of critical questions:
- What is the purpose of this item?
- When was this item last used?
- How frequently is it used?
- Who is the primary user of this item?
- Is it essential for this item to be located here?
For items whose value or necessity is uncertain, a red tag is affixed. This tag typically contains information such as the item description, the date it was tagged, the name of the person who tagged it, and the reason for tagging. These red-tagged items are then moved to a centrally located, designated holding area. This structured approach prevents the premature disposal of potentially valuable items while still removing them from the active workspace.
The Sort phase delivers immediate and visible results. It dramatically frees up valuable physical floor space. More importantly, it reduces the cognitive load on employees by eliminating visual noise and distractions, allowing them to focus more effectively on value-adding tasks.
2. Straighten.
Once the workspace has been decluttered, Seiton or Straighten can begin. It aims to logically and ergonomically arrange all remaining necessary items to ensure they are easily found, used, and returned.
Straighten relies heavily on visual management tools to make the organizational system intuitive and self-sustaining. Effective implementation moves beyond simple arrangement to engineer a workspace that communicates its operating logic.
Key tools include:
- Shadow Boards and Tool Foam: These tools create a visual home for every hand tool. A shadow board has an outline of each tool painted or affixed to a pegboard, making it immediately obvious where a tool belongs and, more importantly, when it is missing. Tool foam, often used in drawers, consists of two-toned foam layers where the outline of each tool is cut from the top layer. The contrasting bottom color is revealed when a tool is removed, providing a clear visual cue that an item is in use or missing.
- Floor Marking and Labeling: The use of durable, industrial-grade floor marking tape and clear, standardized labels is fundamental to Straighten. This practice visually designates specific locations for machinery, pallets, mobile equipment (like pallet jacks), trash receptacles, and works-in-progress. It also defines clear pedestrian walkways and traffic lanes, which significantly improves both workflow and safety.
- Ergonomic Placement: A core principle of Straighten is organizing items based on their frequency of use. Tools and materials used most frequently should be placed closest to the point of use, within easy reach of the operator. This minimizes wasted motion, such as walking, bending, and reaching, which not only improves efficiency but also reduces the risk of ergonomic injuries and physical strain.
3. Shine.
Seiso or Shine involves much more than simple cleaning. It aims to thoroughly clean the work area, equipment, and tools, and to integrate this cleaning activity with regular inspections and proactive preventive maintenance. A critical aspect of Shine is that it is the responsibility of every employee within their workspace, not a task delegated solely to a cleaning crew. This practice fosters a powerful sense of ownership and pride in the work environment. When employees are responsible for the condition of their equipment and area, they become more attuned to their normal operating state.
The true power of the Shine pillar lies in its function as a form of inspection. A clean machine and a spotless work area make abnormalities instantly visible. An oil leak on a freshly painted floor, a small crack in a machine guard, unusual vibrations, or signs of excessive wear become immediately apparent during the cleaning process. This allows for proactive maintenance to be performed before a minor issue escalates into a major failure. This proactive approach prevents costly unplanned downtime, extends the operational lifespan of equipment, and enhances overall safety and reliability.
4. Standardize.
Seiketsu (standardize) is the crucial step that prevents the workplace from regressing to its former chaotic state. It aims to create consistent, documented, and visually intuitive procedures that ensure the principles of Sort, Straighten, and Shine are maintained as the new operational standard.
Standardization is achieved by embedding the new practices into the daily work routine through clear and accessible tools:
- Checklists and Job Cycle Charts: These documents formalize the responsibilities associated with the 5S methodology. A checklist might detail the specific cleaning and inspection tasks to be performed at a workstation at the end of each shift. A job cycle chart can assign specific 5S duties (e.g., "check red tag area," "restock supplies") to specific roles on a daily or weekly schedule, ensuring clear accountability.
- Visual Cues and Controls: Standardization relies heavily on making the correct procedures the easiest ones to follow. This is achieved through consistent visual cues, such as standardized color-coding for different types of materials or zones, clear signage indicating workflows, and labels that provide operating or cleaning instructions directly at the point of use.
- Before-and-After Photos: Displaying visual documentation of the transformation achieved during the initial 5S blitz serves as a powerful and constant reminder of the established standard. These photos help reinforce the new expectations and demonstrate the tangible benefits of the program, motivating teams to maintain the gains.
5. Sustain.
Shitsuke, or sustain, is the most challenging and critical phase of the 5S methodology. It aims to transform the 5S principles from a set of externally imposed rules into a long-term, self-perpetuating habit. Without a comprehensive sustain phase, even the most successful 5S implementations will inevitably fade over time as old habits creep back in.
Sustaining 5S is an active, ongoing process driven by several key factors:
- Visible Leadership Commitment: This is the single most critical factor for long-term success. When managers and executives are visibly and consistently engaged by participating in gemba walks (visits to the actual workplace), personally reviewing audit results, allocating necessary resources, and celebrating successes.
- Ongoing Training and Communication: 5S is not a one-time training event; it requires ongoing training and communication. New employees must be onboarded into the 5S culture, and existing employees need regular reinforcement. Continuous communication through team meetings, newsletters, performance reviews, and visual management boards keeps the principles top-of-mind and allows for the sharing of best practices across the organization.
- Audits and Performance Measurement: Regular, scheduled 5S audits serve as a mechanism for ensuring accountability and driving continuous improvement. These audits should utilize a standardized checklist or scorecard to provide objective, data-driven feedback on compliance levels across various areas. The results can identify areas that are excelling and those that may need additional coaching or resources, creating a crucial feedback loop that fuels the Kaizen cycle.
6. Safety.
Some organizations believe that properly implementing Lean manufacturing procedures based on the 5S framework promotes optimized workplace safety. Others consider safety so vital that they choose to address it as a separate step.
For instance, implementing Sort, Straighten, and Shine will have a measurable impact on workplace safety. These aspects of the 5S methodology can help organize a workplace environment for your staff. Since Shine also includes a tool maintenance component, this step can help prevent equipment-related workplace accidents.
However, some safety practices aren’t addressed explicitly in 5S. An example is that the framework provides no clear direction about the need for proper safety signage.
If you consider this signage a component of a “clean” work environment, your organization will probably address this concern during the Straighten or Shine stage. However, if your team doesn’t share this view, signage may be overlooked as they progress through the 5S process.
5S implementation best practices.
A successful 5S implementation is a structured, strategic project, not an informal cleanup effort. It requires careful planning, dedicated resources, and a phased approach to build momentum and ensure long-term sustainment. The most effective rollouts often mirror the principles of agile development: starting with a small, manageable pilot, gathering feedback, iterating on the process, and then scaling the refined model across the organization.
Getting buy-in from leadership.
This initial phase is the most critical, as it lays the groundwork for everything that follows. Without a solid foundation of leadership support and employee understanding, any 5S initiative is likely to fail. Securing leadership buy-in is the non-negotiable first step. The implementation team must frame the 5S proposal to senior management not as a clean-up project, but as a strategic initiative with a clear and compelling return on investment.
Implementation pilot group.
The implementation of 5S methodology should not be attempted as a facility-wide rollout. A phased approach, starting with a pilot, is essential for testing, learning, and refining the process.
Select a single, well-defined, and manageable pilot area to begin the implementation. This could be a specific work cell, a department, or a particular value stream. Choosing a location with visible challenges and a receptive team can help ensure a successful pilot or test. This approach contains the scope of the initial effort, reduces confusion, and creates a controlled environment for learning and adaptation.
Additionally, one of the most powerful tools in this phase is visual documentation. The team should take extensive "before" photos and videos of the pilot area to capture its initial state. As a final step, the implementation team should conduct a debriefing session with the pilot area team. The goal is to gather direct feedback on what worked well, the challenges encountered, and how the process can be improved. This feedback is then used to refine the implementation approach before it is scaled to other areas.
Scaling implementation.
With a successful pilot and a refined process completed, the organization can proceed to the normalization and scaling phase, which focuses on standardization and sustainability.
- Develop Standards (Standardize): The learnings and best practices from the pilot program are now formalized into clear, simple, and highly visual standards that can be applied across the organization. This includes creating standardized 5S checklists, documenting new work procedures, and developing visual aids (like standardized color codes and label formats) that make the new way of working intuitive and easy to follow.
- Establish Audit Routines (Sustain): To ensure that the new standards are maintained, a system of regular 5S audits must be established. This involves creating a master audit schedule and using standardized digital checklists or scorecards to track compliance in each area. Cross-functional teams should conduct these audits to bring fresh eyes and objectivity to the process. The results of the audits should be posted publicly on visual management boards to create transparency and accountability.
- Phased Rollout: The refined 5S implementation process is now rolled out to the rest of the organization in a planned, phased manner. By scaling the program one area at a time, the organization can ensure that each team receives the necessary attention and resources to be successful, building on the momentum of previous wins.
Benefits of 5S

While the principles of 5S are straightforward, their collective impact on an organization's performance is profound and, importantly, measurable. The benefits are not isolated; they create a powerful feedback loop that generates returns on the initial investment of time and resources. Improved organization in the workplace can lead to greater efficiency, which enhances safety, boosts morale, and improves quality, ultimately contributing to a stronger bottom line. Most case studies demonstrate that organizations recover their investment in 5S within a few months and continue to accrue gains over time.
Save money.
The efficiency and safety gains from 5S translate directly into measurable financial benefits and higher quality output. By optimizing the use of resources—space, materials, and equipment—5S strengthens an organization's bottom line.
- Space Optimization: The Sort and Straighten phases identify significant amounts of previously unusable space.
- Reduced Waste and Defects: An organized environment with standardized, visually managed processes inherently minimizes the potential for errors, rework, and material waste. When the right tool and the right part are in the correct location, the likelihood of using the wrong component or performing a task incorrectly diminishes. This leads to higher first-pass quality, lower scrap rates, and reduced costs associated with defects.
- Improved Maintenance and Equipment Longevity: The Shine pillar's emphasis on cleaning as a form of inspection is a cornerstone of Total Productive Maintenance (TPM). By catching minor issues like leaks or wear early, organizations can perform low-cost preventive maintenance instead of reacting to catastrophic, high-cost equipment breakdowns. This reduces maintenance expenses, minimizes production downtime, and extends the functional lifespan of valuable assets.
Achieve greater productivity.
The most immediate and frequently cited benefit of the 5S methodology is a dramatic improvement in productivity and operational efficiency. By systematically eliminating waste, particularly waste associated with searching and unnecessary motion, 5S enables employees to dedicate more of their time to value-added activities.
- Reduced Search Time: A disorganized workspace forces employees to waste time searching for tools, parts, or information. 5S directly attacks this inefficiency.
- Improved System Efficiency: The cumulative effect of a well-organized and standardized environment can lead to remarkable gains in overall system performance.
Ensure efficient use of space.
By eliminating unnecessary items from a workspace, you can reduce clutter and congestion. This can save employees time getting from one place to another. This will enable your team to transition smoothly from task to task. Additionally, a well-organized workplace can prevent injuries from happening.
Enhance product quality.
By providing the correct tools, employees can provide higher product quality. Setting employees up for success can reduce product creation turnaround time by increasing efficiency in the product lifecycle. This can reduce wasted time or time that employees spend being unproductive. A benefit of enhancing product quality is increased profitability, as it lowers the initial time and resources required to create a product.
Increase safety.
A clean, orderly, and predictable work environment is inherently safer and more positive. The 5S methodology systematically identifies and addresses the root causes of many workplace accidents, contributing significantly to a more engaged and motivated workforce.
- Safety Improvements: By removing clutter, ensuring clear walkways, and eliminating trip hazards, the Sort and Straighten pillars directly reduce the risk of common accidents, such as slips, trips, and falls. The proactive maintenance and inspection activities embedded in the Shine phase help prevent equipment-related accidents before they happen.
- Boosted Employee Morale: A strong correlation exists between the physical work environment and employee morale. Employees who work in a clean, safe, and well-organized space report higher levels of job satisfaction, feel more respected by their employer, and take greater pride in their work. The participatory nature of 5S, where employees are empowered to improve their workspace, is a powerful driver of engagement. This sense of ownership leads to lower rates of absenteeism and employee turnover, creating a more stable and experienced workforce.
Maximize equipment longevity.
The Shine pillar's emphasis on cleaning can detect minor issues, such as leaks or wear, early, allowing organizations to perform low-cost preventive maintenance instead of reacting to catastrophic, high-cost equipment breakdowns. This reduces maintenance expenses, minimizes production downtime, and extends the functional lifespan of valuable assets.
Implement 5S methodology with Workfront.
The 5S methodology provides an organized workplace that helps team members optimize productivity, efficiency, and facility output. The 5S method can help reduce costs, promote workplace safety, improve product quality, increase equipment lifespan, increase productivity, and optimize space utilization.
When you’re ready to embrace this framework, consider how to roll out 5S to your company. The exact approach you use will depend on the size of your company and the existing work management structures you already have in place.
For leaders who want to optimize and centralize their workflows, Workfront connects work to strategy, enabling the management of the entire project lifecycle from start to finish.
To learn how Workfront can help you implement the 5S methodology, watch the overview video.
Recommended for you
https://business.adobe.com/fragments/resources/cards/thank-you-collections/workfront